Metering and Monitoring Functions
Overview
The LTMR controller provides measurement, metering, and monitoring in support of the current, temperature, and ground current trip protection functions. When connected to an LTME expansion module, the LTMR controller also provides voltage and power measurement functions.
Measurement
Overview
The LTMR controller uses these measurements to perform protection, control, monitoring, and logic functions. Each measurement is detailed in this section.
The measurements can be accessed via:
-
a PC running SoMove with the TeSys T DTM
-
an HMI device
-
a PLC via the network port
Line Currents
Description
The LTMR controller measures line currents and provides the value of each phase in amperes and as a percentage of Full Load Current (FLC).
The line currents function returns the rms value in amperes of the phase currents from the three CT inputs:
-
L1: phase 1 current
-
L2: phase 2 current
-
L3: phase 3 current
The LTMR controller performs true rms calculations for line currents up to the seventh harmonic.
Single-phase current is measured from L1 and L3.
Line Current Characteristics
The line currents function has the following characteristics:
Characteristic |
Value |
---|---|
Unit |
A |
Accuracy |
|
Resolution |
0.01 A |
Refresh interval |
100 ms |
Line Current Ratio
The L1, L2, and L3 current ratio parameter provides the phase current as a percentage of FLC.
Line Current Ratio Formulas
The line current value for the phase is compared to the FLC parameter setting, where FLC is FLC1 or FLC2, whichever is active at that time.
Calculated Measurement |
Formula |
---|---|
Line current ratio |
100 x Ln/FLC |
Where:
|
Line Current Ratio Characteristics
The line current ratio function has the following characteristics:
Characteristic |
Value |
---|---|
Unit |
% of FLC |
Accuracy |
Refer to Line Current Characteristics |
Resolution |
1% FLC |
Refresh interval |
100 ms |
Ground Current
Description
The LTMR controller measures ground currents and provides values in Amperes and as a percentage of FLCmin.
-
The internal ground current (Igr∑) is calculated by the LTMR controller from the three line currents measured by the load current transformers. It reports 0 when the current falls below 10% of FLCmin.
-
The external ground current (Igr) is measured by the external ground current sensor connected to Z1 and Z2 terminals.
Configurable Parameters
The control channel configuration has the following configurable parameter settings:
Parameter |
Setting Range |
Factory Setting |
---|---|---|
Ground Current Mode |
|
Internal |
Ground Current Ratio |
|
None |
Ground CT Primary |
|
1 |
Ground CT Secondary |
|
1 |
External Ground Current Formula
The external ground current value depends on the parameter settings:
Calculated Measurement |
Formula |
---|---|
External ground current |
(Current through Z1-Z2) x (Ground CT Primary) / (Ground CT Secondary) |
Ground Current Characteristics
The ground current function has the following characteristics:
Characteristic |
Value |
||
---|---|---|---|
Internal Ground Current (IgrΣ) |
External Ground Current (Igr) |
||
Unit |
A |
A |
|
Accuracy |
|||
LTMR 08xxx |
Igr ≥ 0.3 A |
+/– 10% |
The greater of +/– 5% or +/– 0.01 A |
0.2 A ≤ Igr ≤ 0.3 A |
+/– 15% |
||
0.1 A ≤ Igr ≤ 0.2 A |
+/– 20% |
||
Igr < 0.1 A |
N/A * |
||
LTMR 27xxx |
Igr ≥ 0.5 A |
+/– 10% |
|
0.3 A ≤ Igr ≤ 0.5 A |
+/– 15% |
||
0.2 A ≤ Igr ≤ 0.3 A |
+/– 20% |
||
Igr < 0.2 A |
N/A * |
||
LTMR 100xxx |
Igr ≥ 1.0 A |
+/– 10% |
|
0.5 A ≤ Igr ≤ 1.0 A |
+/– 15% |
||
0.3 A ≤ Igr ≤ 0.5 A |
+/– 20% |
||
Igr < 0.3 A |
N/A * |
||
Resolution |
0.01 A |
0.01 A |
|
Refresh interval |
100 ms |
100 ms |
Ground Current Ratio
The Ground Current Ratio parameter provides the ground current value as a percentage of FLCmin.
Ground Current Ratio Formulas
The ground current value is compared to FLCmin.
Calculated Measurement |
Formula |
---|---|
Ground current ratio |
100 x ground current / FLCmin |
Ground Current Ratio Characteristics
The ground current ratio function has the following characteristics:
Characteristic |
Value |
---|---|
Unit |
0…2,000% of FLCmin |
Accuracy |
Refer to Ground Current Characteristics |
Resolution |
0.1 % FLCmin |
Refresh interval |
100 ms |
Average Current
Description
The LTMR controller calculates average current and provides the value for phase in amperes and as a percentage of FLC.
The average current function returns the rms value of the average current. It returns to 0 when the average current is below 20% of FLCmin.
Average Current Formulas
The LTMR controller calculates the average current using the measured line currents. The measured values are internally summed using the following formula:
Calculated Measurement |
Formula |
---|---|
Average current, three-phase motor |
Iavg = (L1 + L2 + L3) / 3 |
Average current, single-phase motor |
Iavg = (L1 + L3) / 2 |
Average Current Characteristics
The average current function has the following characteristics:
Characteristic |
Value |
|
---|---|---|
Unit |
A |
|
Accuracy |
|
|
Resolution |
0.01 A |
|
Refresh interval |
100 ms |
Average Current Ratio
The Average Current Ratio parameter provides the average current value as a percentage of FLC.
Average Current Ratio Formulas
The average current value for the phase is compared to the FLC parameter setting, where FLC is FLC1 or FLC2, whichever is active at that time.
Calculated Measurement |
Formula |
---|---|
Average current ratio |
100 x lavg / FLC |
Where:
|
Average Current Ratio Characteristics
The average current ratio function has the following characteristics:
Characteristic |
Value |
|
---|---|---|
Unit |
% of FLC |
|
Accuracy |
Refer to Average Current Characteristics |
|
Resolution |
1% FLC |
|
Refresh interval |
100 ms |
Current Phase Imbalance
Description
The current phase imbalance function measures the maximum percentage of deviation between the average current and the individual phase currents.
Formulas
The current phase imbalance measurement is based on imbalance ratio calculated from the following formulas:
Calculated Measurement |
Formula |
---|---|
Imbalance ratio of current in phase 1 (in %) |
Ii1 = (| L1 - Iavg | x 100) / Iavg |
Imbalance ratio of current in phase 2 (in %) |
Ii2 = (| L2 - Iavg | x 100) / Iavg |
Imbalance ratio of current in phase 3 (in %) |
Ii3 = (| L3 - Iavg | x 100) / Iavg |
Current imbalance ratio for three phases (in %) |
Iimb = Max(Ii1, Ii2, Ii3) |
Characteristics
The line current imbalance function has the following characteristics:
Characteristic |
Value |
|
---|---|---|
Unit |
% |
|
Accuracy |
|
|
Resolution |
1% |
|
Refresh interval |
100 ms |
Thermal Capacity Level
Description
The thermal capacity level function uses two thermal models to calculate the amount of thermal capacity used: one for copper stator and rotor windings of the motor and the other for the iron frame of the motor. The thermal model with the maximum utilized capacity is reported.
This function also estimates and displays:
-
The time remaining before a thermal overload trip is triggered (refer to Time to Trip), and
-
The time remaining until the trip condition is cleared after a thermal overload trip has been triggered (refer to Minimum Wait Time).
Trip Current Characteristics
The thermal capacity level function uses one of the following selected trip current characteristics (TCCs):
-
Definite time
-
Inverse thermal (factory setting)
Thermal Capacity Level Models
Both copper and iron models use the maximum measured phase current and the Motor Trip Class parameter value to generate a non-scaled thermal image. The reported thermal capacity level is calculated by scaling the thermal image to FLC.
Thermal Capacity Level Characteristics
The thermal capacity level function has the following characteristics:
Characteristic |
Value |
---|---|
Unit |
% |
Accuracy |
+/– 1% |
Resolution |
1% |
Refresh interval |
100 ms |
Motor Temperature Sensor
Description
The motor temperature sensor function displays:
-
The resistance value in ohms measured by a PTC or NTC resistance temperature sensor.
-
The temperature value in °C or °F measured by a PT100 temperature sensor.
Refer to the product documentation for the specific temperature sensor being used. One of four types of temperature sensors can be used:
-
PTC Binary
-
PT100
-
PTC Analog
-
NTC Analog
Characteristics
The motor temperature sensor function has the following characteristics:
Characteristic |
PT100 Temperature Sensor |
Other Temperature Sensor |
---|---|---|
Unit |
°C or °F, according to the value of the HMI Display Temperature Sensor Degree CF parameter |
Ω |
Accuracy |
+/- 2% |
+/– 2% |
Resolution |
1 °C or 1 °F |
0.1 Ω |
Refresh interval |
500 ms |
500 ms |
Frequency
Description
The frequency function provides the value measured based on the line voltage measurements. If the frequency is unstable (+/– 2 Hz variations), the value reported is 0 until the frequency stabilizes.
If no LTME expansion module is present, the frequency value is 0.
Characteristics
The frequency function has the following characteristics:
Characteristic |
Value |
---|---|
Unit |
Hz |
Accuracy |
+/– 2% |
Resolution |
0.1 Hz |
Refresh interval |
30 ms |
Line-to-Line Voltages
Description
The line-to-line voltages function provides the rms value of the phase-to-phase voltage (V1 to V2, V2 to V3, and V3 to V1):
-
L1-L2 voltage: phase 1 to phase 2 voltage
-
L2-L3 voltage: phase 2 to phase 3 voltage
-
L3-L1 voltage: phase 3 to phase 1 voltage
The expansion module performs true rms calculations for line-to-line voltage up to the seventh harmonic.
Single phase voltage is measured from L1 and L3.
Characteristics
The line-to-line voltages function has the following characteristics:
Characteristic |
Value |
---|---|
Unit |
Vac |
Accuracy |
+/- 1% |
Resolution |
1 Vac |
Refresh interval |
100 ms |
Line Voltage Imbalance
Description
The line voltage imbalance function displays the maximum percentage of deviation between the average voltage and the individual line voltages.
Formulas
The line voltage imbalance calculated measurement is based on the following formulas:
Calculated Measurement |
Formula |
---|---|
Imbalance ratio of voltage in phase 1 in % |
Vi1 = 100 x | V1 - Vavg | / Vavg |
Imbalance ratio of voltage in phase 2 in % |
Vi2 = 100 x | V2 - Vavg | / Vavg |
Imbalance ratio of voltage in phase 3 in % |
Vi3 = 100 x | V3 - Vavg | / Vavg |
Voltage imbalance ratio for three phases in % |
Vimb = Max (Vi1, Vi2, Vi3) |
Where:
|
Characteristics
The line voltage imbalance function has the following characteristics:
Characteristic |
Value |
---|---|
Unit |
% |
Accuracy |
+/– 1.5% |
Resolution |
1% |
Refresh interval |
100 ms |
Average Voltage
Description
The LTMR controller calculates average voltage and provides the value in volts. The average voltage function returns the rms value of the average voltage.
Formulas
The LTMR controller calculates average voltage using the measured line-to-line voltages. The measured values are internally summed using the following formula:
Calculated Measurement |
Formula |
---|---|
Average voltage, three-phase motor |
Vavg = (L1-L2 voltage + L2-L3 voltage + L3-L1 voltage) / 3 |
Average voltage, single-phase motor |
Vavg = L3-L1 voltage |
Characteristics
The average voltage function has the following characteristics:
Characteristic |
Value |
---|---|
Unit |
Vac |
Accuracy |
+/- 1% |
Resolution |
1 Vac |
Refresh interval |
100 ms |
Power Factor
Description
The power factor function displays the phase displacement between the phase currents and phase voltages.
Formula
The Power Factor parameter (also called cosine phi or cos ϕ) represents the absolute value of the ratio of Active Power to Apparent Power.
Characteristics
The power factor function has the following characteristics:
Characteristic |
Value |
---|---|
Accuracy |
+/- 10% for cos ϕ ≥ 0.6 |
Resolution |
0.01 |
Refresh interval |
30 ms (typical)* |
Active Power and Reactive Power
Description
The calculation of the active power and reactive power is based on the:
-
Average rms phase voltage of L1, L2, L3
-
Average rms phase current of L1, L2, L3
-
Power factor
-
Number of phases
Formulas
Active power, also known as true power, measures average rms power. It is derived from the following formulas:
Calculated Measurement |
Formula |
---|---|
Active power for three-phase motor |
√3 x lavg x Vavg x cosϕ |
Active power for single-phase motor |
lavg x Vavg x cosϕ |
Where:
|
The reactive power measurement is derived from the following formulas:
Calculated Measurement |
Formula |
---|---|
Reactive power for three-phase motor |
√3 x lavg x Vavg x sinϕ |
Reactive power for single-phase motor |
lavg x Vavg x sinϕ |
Where:
|
Characteristics
The active and reactive power functions have the following characteristics:
Characteristic |
Active Power |
Reactive Power |
---|---|---|
Unit |
kW |
kVAR |
Accuracy |
+/- 15% |
+/- 15% |
Resolution |
0.1 kW |
0.1 kVAR |
Refresh interval |
100 ms |
100 ms |
Active Power Consumption and Reactive Power Consumption
Description
The active and reactive power consumption functions display the accumulated total of the active and reactive electrical power delivered, and used or consumed by the load.
Characteristics
The active and reactive power consumption functions have the following characteristics:
Characteristic |
Active Power Consumption |
Reactive Power Consumption |
---|---|---|
Unit |
kWh |
kVARh |
Accuracy |
+/- 15% |
+/- 15% |
Resolution |
1 kWh |
1 kVARh |
Refresh interval |
100 ms |
100 ms |
System and Device Monitoring Trips
Overview
The LTMR controller and the LTME expansion module detect trips which affect the LTMR controller ability to work properly (internal controller check and check of communications, wiring, and configuration detected errors).
The system and device monitoring trip records can be accessed via:
-
A PC running SoMove with the TeSys T DTM
-
An HMI device
-
A PLC via the network port
Controller Internal Trip
Description
The LTMR controller detects and records trips that are internal to the device itself. Internal trips can be either major or minor. Major and minor trips can change the state of output relays. Cycling power to the LTMR controller may clear an internal trip.
When an internal trip occurs, the Controller Internal Trip parameter is set.
Major Internal Trips
During a major trip, the LTMR controller is unable to reliably execute its own programming and can only attempt to shut itself down. During a major trip, communication with the LTMR controller is not possible. Major internal trips include:
-
Stack overflow trip
-
Stack underflow trip
-
Watchdog time-out
-
Firmware checksum detected error
-
CPU detected error
-
Internal temperature trip (at 100 °C/212 °F)
-
RAM test detected error
Minor Internal Trips
Minor internal trips indicate that the data being provided by the LTMR controller is unreliable and protection could be compromised. During a minor trip, the LTMR controller continues to attempt to monitor status and communications, but does not accept any start commands and Custom Logic functions are halted. During a minor trip condition, the LTMR controller continues to detect and report major trips, but not additional minor trips. Minor internal trips include:
-
Internal network communications trip
-
EEPROM detected error
-
A/D out of range detected error
-
Reset button stuck
-
Internal temperature trip (at 85 °C/185 °F)
-
Invalid configuration detected error (conflicting configuration)
-
Detected improper logic function action (for example, attempting to write to a read-only parameter)
Controller Internal Temperature
Description
The LTMR controller monitors its Controller Internal Temperature, and reports alarm, minor trip, and major trip conditions. Trip detection cannot be disabled. Alarm detection can be enabled or disabled.
The controller retains a record of the highest attained internal temperature.
Characteristics
The Controller Internal Temperature measured values have the following characteristics:
Characteristic |
Value |
|
---|---|---|
Unit |
°C |
|
Accuracy |
+/- 4 °C (+/- 7.2 °F) |
|
Resolution |
1 °C (1.8 °F) |
|
Refresh interval |
100 ms |
Parameters
The Controller Internal Temperature function includes one editable parameter:
Parameter |
Setting Range |
Factory Setting |
---|---|---|
Controller internal temperature alarm enable |
|
Enable |
The Controller Internal Temperature function includes the following fixed alarm and trip thresholds:
Condition |
Fixed Threshold Value |
Sets Parameter |
|
---|---|---|---|
Internal temperature alarm |
80 °C (176 °F) |
Controller Internal Temperature Alarm |
|
Internal temperature minor trip |
85 °C (185 °F) |
Controller Internal Trip |
|
Internal temperature major trip |
100 °C (212 °F) |
An alarm condition ceases when LTMR Controller Internal Temperature falls below 80 °C (176 °F).
Block Diagram
Maximum Internal Controller Temperature
The Controller Internal Temperature Max parameter contains the highest internal temperature, expressed in °C, detected by the LTMR controller’s internal temperature sensor. The LTMR controller updates this value whenever it detects an internal temperature greater than the current value.
The maximum internal temperature value is not cleared when factory settings are restored using the Clear All Command, or when statistics are reset using a Clear Statistics Command.
Control Command Trip Diagnostic
Description
The LTMR controller performs diagnostic tests that detect and monitor the proper functionality of control commands.
There are four control command diagnostic functions:
-
Start Command Check
-
Run Check
-
Stop Command Check
-
Stop Check
Parameter Settings
All four diagnostic functions are enabled and disabled as a group. The configurable parameter settings are:
Parameters |
Setting Range |
Factory Setting |
---|---|---|
Diagnostic Trip Enable |
Yes/No |
Yes |
Diagnostic Alarm Enable |
Yes/No |
Yes |
Start Command Check
The Start Command Check begins after a Start command, and causes the LTMR controller to monitor the main circuit to ensure that current is flowing.
-
The Start Command Check reports a Start Command trip or alarm if current is not detected after a delay of 1 second.
-
The Start Command Check condition ends if the motor is in Start or Run state (lavg > 20% FLC) at the one second delay point, then begins the Run Check.
Run Check
The Run Check causes the LTMR controller to continuously monitor the main circuit to ensure current is flowing.
-
The Run Check reports a trip or alarm if average phase current is not detected for longer than 0.5 seconds without a Stop command.
-
The Run Check ends when a Stop command executes.
Stop Command Check
The Stop Command Check begins after a Stop command, and causes the LTMR controller to monitor the main circuit and ensure that no current is flowing.
-
The Stop Command Check reports a trip or alarm if current is detected after a delay of 1 second.
-
The Stop Command Check ends if the LTMR controller detects that the current is equal or less than 5% of FLCmin.
Stop Check
The Stop Check causes the LTMR controller to continuously monitor the main circuit to ensure that no current is flowing.
-
The Stop Check reports a Stop Check trip or alarm if average phase current is detected for longer than 0.5 seconds after a Stop command.
-
The Stop Check condition ends when a Run command executes.
Timing Sequence
The following diagram is an example of the timing sequence for the Start Command Check and Stop Command Check:
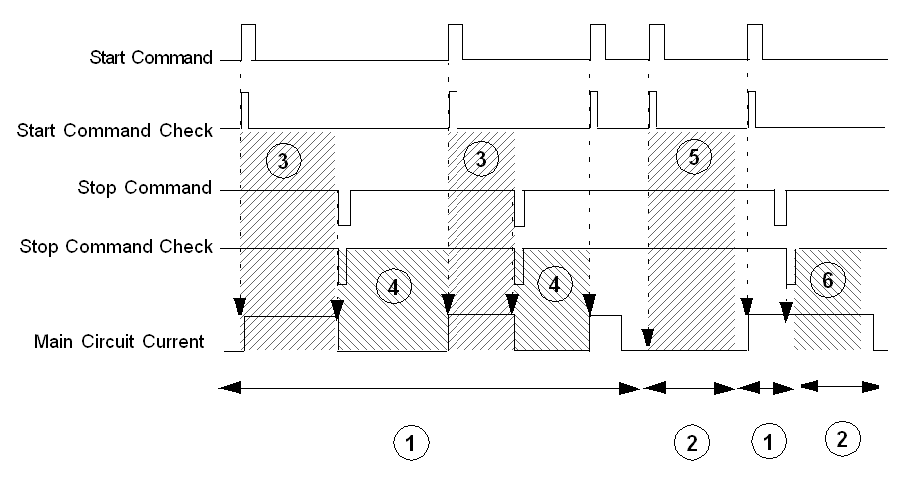
1 Normal operation
2 Trip or alarm condition
3 The LTMR controller monitors the main circuit to detect current
4 The LTMR controller monitors the main circuit to detect no current
5 The LTMR controller reports a Start Command Check trip and/or alarm if current is not detected after 1 second
6 The LTMR controller reports a Stop Command Check trip and or alarm if current is detected after 1 second
The following diagram is an example of the timing sequence for the Run Check and Stop Check:

1 Normal operation
2 Trip or alarm condition
3 After the motor enters the run state, the LTMR controller continuously monitors the main circuit to detect current until a Stop command is given or the function is disabled
4 The LTMR controller continuously monitors the main circuit to detect no current until a Start command is given or the function is disabled
5 The LTMR controller reports a Run Check trip and/or alarm if the current is not detected for longer than 0.5 seconds without a Stop command
6 The LTMR controller reports a Stop Check trip or alarm if the current is detected for longer than 0.5 seconds without a Start command
7 No current flowing for less than 0.5 seconds
8 Current flowing for less than 0.5 seconds
Wiring Trips
Description
The LTMR controller checks external wiring connections and reports a trip when it detects incorrect or conflicting external wiring. The LTMR controller can detect four wiring errors:
-
CT Reversal Detected Error
-
Phase Configuration Detected Error
-
Motor Temperature Sensor Wiring Detected Errors (short-circuit or open-circuit)
If LTMR controller is connected on the left port of LTME expansion module, the frequency measurement will be wrong. Hence, it is advised to use the LTMCC004 connecting jumper to avoid trips.
Enabling Trip Detection
Wiring diagnostics are enabled using the following parameters:
Protection |
Enabling Parameters |
Setting Range |
Factory Setting |
---|---|---|---|
CT Reversal |
Wiring Trip Enable |
|
Yes |
Phase Configuration |
Motor Phases, if set to single-phase |
|
three phase |
Motor Temperature Sensor Wiring |
Motor Temperature Sensor Type, if set to a sensor type, and not to None |
|
None |
CT Reversal Detected Error
When individual external load CTs are used, they must all be installed in the same direction. The LTMR controller checks the CT wiring and reports a detected error if it detects one of the current transformers is wired backwards when compared to the others.
This function can be enabled and disabled.
Phase Configuration Detected Error
The LTMR controller checks all three motor phases for On Level current, then checks the Motor Phases parameter setting. The LTMR controller reports a detected error if it detects current in phase 2 if the LTMR controller is configured for single-phase operation.
This function is enabled when the LTMR controller is configured for single-phase operation. It has no configurable parameters.
Motor Temperature Sensor Detected Errors
When the LTMR controller is configured for motor temperature sensor protection, the LTMR controller provides short-circuit and open-circuit detection for the temperature sensing element.
The LTMR controller signals a detected error when calculated resistance at the T1 and T2 terminals:
-
Falls below the fixed short-circuit detection threshold (trip code = 34), or
-
Exceeds the fixed open-circuit detection threshold (trip code = 35).
The trip must be reset according to the configured Reset Mode: manual, automatic, or remote.
Short-circuit and open-circuit detection thresholds have no trip time delay. There are no alarms associated with the short-circuit and the open-circuit detection.
Short-circuit and open-circuit detection of the motor temperature sensing element is available for all operating states.
This protection is enabled when a temperature sensor is employed and configured, and cannot be disabled.
The motor temperature sensor function has the following characteristics:
Characteristic |
Value |
|
---|---|---|
Unit |
Ω |
|
Normal operating range |
15…6500 W |
|
Accuracy |
at 15 Ω: +/– 10% at 6500 Ω: +/– 5% |
|
Resolution |
0.1 Ω |
|
Refresh interval |
100 ms |
The fixed thresholds for the open-circuit and short-circuit detection functions are:
Detection Function |
Fixed Results For PTC Binary, or PT100, or PTC/NTC Analog |
Accuracy |
|
---|---|---|---|
Short-circuit detection |
threshold |
15 Ω |
+/– 10% |
re-closing |
20 Ω |
+/– 10% |
|
Open-circuit detection |
threshold |
6500 Ω |
+/– 5% |
re-closing |
6000 Ω |
+/– 5% |
Configuration Checksum
Communication Loss
Description
The LTMR controller monitors communication through:
-
The network port
-
The HMI port
Network Port Parameter Settings
The LTMR controller monitors network communication creates both a trip and an alarm report when the network communications are lost.
-
On LTMR Ethernet controllers configured with EtherNet/IP or Modbus/TCP communication protocol, the communication loss is detected if no communication exchanges occurred with the Primary IP for a time period equal to, or longer than, the network port communication loss timeout. Primary IP must be configured to allow detection of the communication loss.
-
On LTMR Modbus controllers, the communication loss is detected if no communication exchanges occurred for a time period equal to, or longer than, the network port comm loss timeout.
-
On LTMR PROFIBUS DP, CANopen, or DeviceNet controllers, the communication loss is detected as part of the protocol management, without specific adjustable parameters.
The network port communications have the following configurable settings:
Parameter |
Setting Range |
Factory Setting |
---|---|---|
Network port trip enable |
Enable/Disable |
Disable |
Network port alarm enable |
Enable/Disable |
Disable |
Network port comm loss timeout (for Ethernet and Modbus controller) |
0.01...99.99 s In increments of 0.01 s |
2 s |
Network port fallback setting*(1) |
|
O.1, O.2 off |
Primary IP address (for Ethernet controller only) |
0.0.0.0 to 255.255.255.255 |
0.0.0.0 |
HMI Port Parameter Settings
The LTMR controller monitors HMI port communications and reports both an alarm and a trip if no valid communication has been received by the HMI port for longer than 7 seconds.
The HMI port communication has the following fixed and configurable settings:
Parameter |
Setting Range |
Factory Setting |
---|---|---|
HMI port trip enable |
Enable/Disable |
Disable |
HMI port alarm enable |
Enable/Disable |
Disable |
HMI port fallback setting* |
|
O.1, O.2 off |
Fallback Condition
When the communication between the LTMR controller and either the network or the HMI is lost, the LTMR controller is in a fallback condition. When the communication recovers, the fallback condition is no longer applied by the LTMR controller.
The behavior of logic outputs O.1 and O.2 when the LTMR controller is in fallback condition is determined by:
-
The operating mode (refer to Operating Modes).
-
The Network Port Fallback Setting and HMI Port Fallback Setting parameters.
Fallback setting selection can include:
Port Fallback Setting |
Description |
---|---|
Hold (O.1, O.2) |
Directs the LTMR controller to hold the state of logic outputs O.1 and O.2 as of the time of the communication loss. |
Run |
Directs the LTMR controller to perform a Run command for a 2-step control sequence on the communication loss. |
O.1, O.2 Off |
Directs the LTMR controller to turn off both logic outputs O.1 and O.2 following a communication loss. |
O.1, O.2 On |
Directs the LTMR controller to turn on both logic outputs O.1 and O.2 following a communication loss. |
O.1 On |
Directs the LTMR controller to turn on only logic output O.1 following a communication loss. |
O.2 On |
Directs the LTMR controller to turn on only logic output O.2 following a communication loss. |
The following table indicates which fallback options are available for each operating mode:
Port Fallback Setting |
Operating Mode |
|||||
---|---|---|---|---|---|---|
Overload |
Independent |
Reverser |
2-step |
2-speed |
Custom |
|
Hold (O.1, O.2) |
Yes |
Yes |
Yes |
Yes |
Yes |
Yes |
Run |
No |
No |
No |
Yes |
No |
No |
O.1, O.2 Off |
Yes |
Yes |
Yes |
Yes |
Yes |
Yes |
O.1, O.2 On |
Yes |
Yes |
No |
No |
No |
Yes |
O.1 On |
Yes |
Yes |
Yes |
No |
Yes |
Yes |
O.2 On |
Yes |
Yes |
Yes |
No |
Yes |
Yes |
Time to Trip
Description
When a thermal overload condition exists, the LTMR controller reports the time to trip before the trip occurs in the Time To Trip parameter.
When the LTMR controller is not in a thermal overload condition, to avoid the appearance of being in a trip state, the LTMR controller reports the time to trip as 9999.
If the motor has an auxiliary fan and the Motor Aux Fan Cooled parameter has been set, the cooling period is four times shorter.
Characteristics
The time to trip function has the following characteristics:
Characteristic |
Value |
---|---|
Unit |
s |
Accuracy |
+/– 10% |
Resolution |
1 s |
Refresh interval |
100 ms |
LTMR Configuration Trip
Description
The LTMR controller checks the Load CT parameters set in configuration mode.
An LTMR configuration trip is detected when the Load CT Primary, Load CT Secondary, and Load CT Multiple Passes parameters are not valid, and generates a System and Device Monitoring Trip. The trip condition is cleared once the parameters are correct. The LTMR controller remains in configuration mode as long as the parameters are not valid.
LTME Configuration Trip and Alarm
Description
The LTMR controller checks the presence of the LTME expansion module. Its absence generates a System and Device Monitoring Trip.
LTME Configuration Trip
LTME configuration trip:
-
If LTME based protection trips are enabled but no LTME expansion module is present, this will cause an LTME configuration trip.
-
It does not have any delay setting.
-
The trip condition clears when no protection trip requiring an LTME is enabled, or when the LTMR has been power-cycled with an appropriate LTME being present.
LTME Configuration Alarm
LTME configuration alarm:
-
If LTME based protection alarms are enabled but no LTME expansion module is present, this will cause an LTME configuration alarm.
-
The alarm clears when no protection alarm requiring an LTME is enabled, or when the LTMR has been power-cycled with an appropriate LTME being present.
External Trip
Description
The LTMR controller has an external trip feature, which detects if an error happened on an external system linked to it.
An external trip is triggered by setting a bit in the custom logic command register 1 (see following table). This external trip sets the controller into a trip state based on different parameters in the system.
An external trip can be reset only by clearing the external trip bit in the register.
External Trip Parameter Settings
Parameter |
Description |
---|---|
Custom logic external trip command |
The value is written |
External system trip |
Reads Custom logic external trip command parameter |
Trip code |
Number is 16: External trip set by program customized with custom logic editor |
Trip and Alarm Counters
Overview
The LTMR controller counts and records the number of trips and alarms that occur. In addition, it counts the number of auto-reset attempts. This information can be accessed to assist with system performance and maintenance.
Trip and alarm counters can be accessed via:
-
A PC running SoMove with the TeSys T DTM
-
An HMI device
-
A PLC via the network port
Introducing Trip and Alarm Counters
Detecting Alarms
If an alarm detection function is enabled, the LTMR controller detects an alarm immediately when the monitored value rises above, or falls below, a threshold setting.
Detecting Trips
Before the LTMR controller detects a trip, certain preconditions must exist. These conditions can include
-
The trip detecting function must be enabled,
-
A monitored value (for example, current, voltage, or thermal resistance) must rise above, or fall below, a threshold setting,
-
The monitored value must remain above or below the threshold setting for a specified time duration.
Counters
When a trip is detected, the LTMR controller increments at least two counters:
-
A counter for the specific trip, and
-
A counter for all trips.
When an alarm is detected, the LTMR controller increments a single counter for all alarms. However, when the LTMR controller detects a thermal overload alarm, it also increments the thermal overload alarms counter.
A counter contains a value from 0 to 65,535 and increments by a value of 1 when a trip, alarm, or reset event is detected. A counter stops incrementing when it reaches a value of 65,535.
When a trip is automatically reset, the LTMR controller increments only the auto-resets counter. Counters are saved on power loss.
Clearing Counters
All trip and alarm counters are reset to 0 by executing the Clear Statistics Command or Clear All Command.
All Trips Counter
All Alarms Counter
Auto-Reset Counter
Description
The Auto-Reset Count parameter contains the number of times the LTMR controller unsuccessfully attempted to auto-reset a trip. This parameter is used for the three auto-reset trip groups.
If an auto-reset attempt is successful (defined as the same trip not recurring within 60 s), this counter is reset to zero. If a trip is reset either manually or remotely, the counter is not incremented.
For information on trip management, refer to Trip Management and Clear Commands.
Protection Trips and Alarms Counters
Protection Trip Counts
Protection trip counters include:
-
Current Phase Imbalance Trips Count
-
Current Phase Loss Trips Count
-
Current Phase Reversal Trips Count
-
Ground Current Trips Count
-
Jam Trips Count
-
Long Start Trips Count
-
Motor Temp Sensor Trips Count
-
Over Power Factor Trips Count
-
Overcurrent Trips Count
-
Overpower Trips Count
-
Overvoltage Trips Count
-
Thermal Overload Trips Count
-
Under Power Factor Trips Count
-
Undercurrent Trips Count
-
Underpower Trips Count
-
Undervoltage Trips Count
-
Voltage Phase Imbalance Trips Count
-
Voltage Phase Loss Trips Count
-
Voltage Phase Reversal Trips Count
Protection Alarm Counts
The Thermal Overload Alarms Count parameter contains the total number of alarms for the thermal overload protection function.
When any alarm occurs, including a thermal overload alarm, the LTMR controller increments the Alarms Count parameter.
Control Command Trip Counter
Description
A Diagnostic Trip occurs when the LTMR controller detects any of the following control command detected errors:
-
Start Command Check detected errors
-
Stop Command Check detected errors
-
Stop Check detected errors
-
Run Check detected errors
For information on these control command functions, refer to Control Command Trip Diagnostic.
Wiring Trips Counter
Description
The Wiring Trips Count parameter contains the total number of the following wiring trips that have occurred since the Clear Statistics Command last executed:
-
Wiring Trip, which is triggered by a:
-
CT Reversal Detected Error
-
Phase Configuration Detected Error
-
Motor Temperature Sensor Wiring Detected Error
-
-
Voltage Phase Reversal Trip
-
Current Phase Reversal Trip
The LTMR controller increments the Wiring Trips Count parameter by a value of 1 each time any one of the above three trips occurs. For information on detected connection errors and related trips, refer to Wiring Trips.
Communication Loss Counters
Description
Trips detected for the following communication functions:
Counter |
Contains |
---|---|
HMI Port Trips Count |
The number of times communications via the HMI port was lost. |
Network Port Internal Trips Count |
The number of internal trips experienced by the network module, reported by the network module to the LTMR controller. |
Network Port Config Trips Count |
The number of major trips experienced by the network module, exclusive of network module internal trips, reported by the network module to the LTMR controller. |
Network Port Trips Count |
The number of times communications via the network port was lost. |
Internal Trip Counters
Description
Trips detected for the following internal trips:
Counter |
Contains |
---|---|
Controller Internal Trips Count |
The number of major and minor internal trips. For information on internal trips, refer to Controller Internal Trip. |
Internal Port Trips Count |
The number of LTMR controller internal communication trips, plus the number of unsuccessful attempts to identify the network communication module. |
Trip History
Trip History
The LTMR controller stores a history of LTMR controller data that was recorded at the time of the last five trips. Trip n-0 contains the most recent trip record, and trip n-4 contains the oldest retained trip record.
Each trip record includes:
-
Trip Code
-
Date and Time
-
Value of Settings
-
Motor Full Load Current Ratio (% of FLCmax)
-
-
Value of Measurements
-
Thermal Capacity Level
-
Average Current Ratio
-
L1, L2, L3 Current Ratio
-
Ground Current Ratio
-
Full Load Current Max
-
Current Phase Imbalance
-
Voltage Phase Imbalance
-
Power Factor
-
Frequency
-
Motor Temp Sensor
-
Average Voltage
-
L3-L1 Voltage, L1-L2 Voltage, L2-L3 Voltage
-
Active Power
-
Motor History
Overview
The LTMR controller tracks and saves motor operating statistics.
Motor statistics can be accessed using:
-
A PC running SoMove with the TeSys T DTM
-
An HMI device
-
A PLC via the network port.
Motor Starts Counters
Description
The LTMR controller tracks motor starts and records the data as a statistic that can be retrieved for operational analysis. The following statistics are tracked:
-
Motor Starts Count
-
Motor LO1 Closings Count (logic output O.1 starts)
-
Motor LO2 Closings Count (logic output O.2 starts)
The Clear Statistics Command resets the Motor Starts Count parameter to 0.
Motor Starts Per Hour Counter
Description
The LTMR controller tracks the number of motor starts during the past hour and records this figure in the Motor Starts Per Hour Count parameter.
The LTMR controller sums start in 5 minutes intervals with an accuracy of 1 interval (+ 0/– 5 minutes), which means that the parameter will contain the total number of starts within either the previous 60 minutes or the previous 55 minutes.
This function is used as a maintenance function to avoid thermal strain on the motor.
Characteristics
The motor starts per hour function has the following characteristics:
Characteristic |
Value |
---|---|
Accuracy |
5 minutes (+ 0/– 5 minutes) |
Resolution |
5 minutes |
Refresh interval |
100 ms |
Load Sheddings Counter
Description
The Load Sheddings Count parameter contains the number of times the load sheddings protection function has been activated since the last Clear Statistics Command.
For information on the Load Sheddings protection function, refer to Load Shedding.
Auto Restart Counters
Description
There are three types of counting statistics:
-
Auto restart immediate count
-
Auto restart delayed count
-
Auto restart manual count
For information on the Auto restart protection function, refer to Automatic Restart.
Motor Last Start Current Ratio
Description
The LTMR controller measures the maximum current level reached during the last start of the motor and reports the value in the Motor Last Start Current Ratio parameter for analysis of the system for maintenance purposes.
This value may also be used to help configure the long start threshold setting in the long start protection function.
The value is not stored in the non-volatile memory: it is lost at a power cycle.
Characteristics
The motor last start current ratio function has the following characteristics:
Characteristic |
Value |
---|---|
Unit |
% of FLC |
Accuracy |
|
Resolution |
1% FLC |
Refresh interval |
100 ms |
Motor Last Start Duration
Description
The LTMR controller tracks the duration of the last motor start and reports the value in the Motor Last Start Duration parameter for analysis of the system for maintenance purposes.
This value may also be useful in setting the long start delay timeout used in the long start and definite trip overload protection functions.
The value is not stored in the non-volatile memory: it is lost at a power cycle.
Characteristics
The motor last start duration function has the following characteristics:
Characteristic |
Value |
---|---|
Unit |
s |
Accuracy |
+/– 1% |
Resolution |
1 s |
Refresh interval |
1 s |
Operating Time
System Operating Status
Overview
The LTMR controller monitors the motor operating state and the minimum time to wait to restart the motor.
The Motor states can be accessed via:
-
A PC running SoMove with the TeSys T DTM
-
An HMI device
-
A PLC via the network port
Motor State
Description
The LTMR controller tracks the motor state and reports the following states by setting the corresponding boolean parameters:
Motor state |
Parameter |
---|---|
Run |
Motor Running |
Ready |
System Ready |
Start |
Motor Starting |
Minimum Wait Time
Description
The LTMR controller tracks the time remaining to restart the motor according to one of the following events:
-
Transition time
If more than one timer is active, the parameter displays the maximum timer, which is the minimum wait for the trip response or the control function to reset.
Characteristics
The Minimum Wait Time function has the following characteristics:
Characteristic |
Value |
---|---|
Unit |
s |
Accuracy |
±1% |
Resolution |
1 s |
Refresh interval |
1 s |